İş Yerinde
İş Yerinde
Job Type
Full-Time
Position Level
Specialist
Department
Quality
Quality
Application Count
471 application
Job Type
Full-Time
Position Level
Specialist
Application Count
471 application
Department
Quality
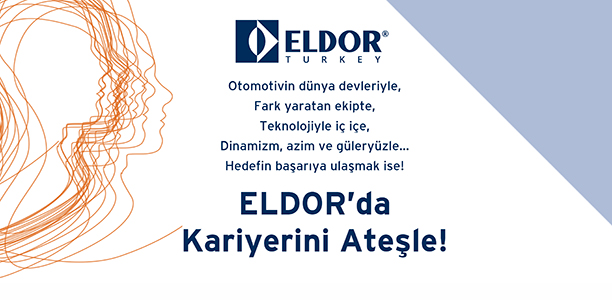
QUALIFICATIONS AND JOB DESCRIPTION
Eldor Corporation, as an international Italian Company with promising future in Turkey operations, produce electronic components for world's leading Automotive Companies.
We are looking for young, dynamic, enthusiastic candidates who are ready to take challenge, improve themselves and team members.
Job Description
- As a Process Quality Engineer at Eldor, with focus on increasing the organizations knowledge and use of quality core tools, you will serve as the voice and defender of our customers within the organization during the development and series production phases and report to Process Quality Chief.
- Your primary role will be to ensure that both products and processes comply with regulatory and organizational standards, meeting and exceeding the high expectations of our customers in all aspects of our operations.
- By consistently wearing the 'customer hat,' you will drive our quality assurance processes and champion continuous improvement initiatives that enhance customer satisfaction and loyalty.
- Your expertise will help identify and implement quality improvements, increasing defect detection, enhancing escape containment, and supporting robust root cause and corrective action processes.
- Lead with a “hands-on mentality”, understanding that quality is the cornerstone of all key processes within our manufacturing company. Oversee critical quality assurance activities, ensuring seamless integration with overall operations.
- Goal: Drive the factory towards operational excellence and sustainable growth through a “quality-centric approach” while working collaboratively with internal teams, including Production, Process Engineering, Maintenance, Failure Analysis Laboratory, R&D, Logistics and Customer Quality team, to foster a competitive quality advantage.
Required Qualifications:
- Bachelor's degree in a relevant engineering field
- At least 2 years in engineering, manufacturing, and/or quality systems
- Computer literate with all Microsoft Office packages
- Effective communication skills, ensuring clarity and understanding across diverse teams
- Hands on work ethic
- Ability to work/lead independently
- Ability to partner with others on projects
- Good written/verbal communication and reporting skill in English
Preferred Qualifications:
- Proven analytical and problem-solving abilities (primarily “8D”), with a preference for knowledge in statistical analysis methods
- 3+ years of experience working in highly regulated sectors such as automotive, defense, or similar industries
- Quality Engineering experience including DOE, CAPA, LEAN, 5S’s and Six Sigma (6 ?).
- Experience in spearheading innovative projects with cross-functional teams, leveraging Industry 4.0, data analytics, and AI technologies within the quality domain. These initiatives should have demonstrated the ability to enhance efficiency, reduce costs, and optimize quality through data-driven decision-making
Responsibilities:
- During the APQP phase, verify the Control Plan in correlation with the Process Flow diagram, PFMEA and compare with current process. Do the same after SOP if any process change occurs and drive engineering team to modify if necessary. Provide support in the use of quality core tools (FMEA, CP, MSA, SPC, PPAP, 8D, etc.,).
- Support the PPAP process, ensuring all responsible departments complete their tasks accurately and on schedule, and support the preparation of customer-specific documentation. Additionally, evaluate MSA & SPC results, and drive team improvements when results are not meeting the expected standards.
- Develop, maintain instructions and related documentation that detail the methods and criteria for control activities as outlined in the control plans.
- Serve as the first contact for customer concerns, convene and lead cross-functional team members to identify the root cause, and implement preventive/corrective actions with correct tools 8D, A3, 5Why, Ishikawa, 6 Sigma- Statistical tools, etc. and conduct a risk analysis by the process/product data.
- Have the authority to stop a line on Production and stop the delivery in case the PPM levels exceeds the predefined limits or any product/process specification is not meeting requirements.
- Lead the non-conformance tracking and reporting system to enhance response times to quality incidents. Streamline problem-solving techniques by standardizing processes and integrating structured methodologies such as 8D, Lean Six Sigma A3, 5Why, Ishikawa etc., focusing on reducing the time required to resolve technical and process-related non-conformances and minimizing recurring issues for Internal&External NCs by leading and supporting engineering and production team.
- Monitor PPM and scrap rates daily for assigned processes and products, conduct data analysis to identify trends and areas for improvement, and ensure a 'data-driven' mentality is upheld. Lead daily meetings with relevant teams to discuss findings, collaborate on necessary actions, and use statistical data to highlight opportunities for improvement. Ensure that actions are documented in the system, followed through to completion, and aimed at maintaining quality standards, reducing defects, and improving process efficiency.
- Monitor, analyze and report on facility key performance indicators/objectives and associated improvement action plans.
- Prepare weekly and monthly Quality Reporting and lead/conduct weekly executive quality meeetings for Scrap&PPM&NCr status and actions.
- Monitor Lessons Learned process outputs/proposals/applied cases for sister companies and evaluate applicability on your process. Initiate LL proposals for your processes in the same manner with contribution of engineering team and share on system.
- Performing LPA Audits according to plan, support on product and process audits with Auditing&Quality System Team according to IATF16949 standard and VDA 6.3&6.5 requirements.
- Actively participate in audits, including customer surveys and on-site reviews by customers, regulators, and internal networks.
- Develop and implement training procedures for quality assurance personnel.
- Evaluate your team performance and report.
Preferred Candidate
Mühendis pozisyonu ile ilgili daha detaylı bilgi almak ya da diğer iş fırsatlarını incelemek için aşağıdaki sayfaları inceleyebilirsiniz.
Mühendis Mühendis Maaşları Mühendis Nasıl Olunur? Mühendis Nedir? Mühendis İş İlanlarıHakkımızda
ELDOR Elektronik ve Plastik Malzemeleri Üretim ve Ticaret Ltd. Şti. ELDOR İzmir AFZ, merkezi İtalya, Orsenigo’da bulunan ulus
Şirket Sayfasına GitŞirketin Aydınlatma Metni
Detaylı BilgiMühendis pozisyonu ile ilgili daha detaylı bilgi almak ya da diğer iş fırsatlarını incelemek için aşağıdaki sayfaları inceleyebilirsiniz.
Mühendis Mühendis Maaşları Mühendis Nasıl Olunur? Mühendis Nedir? Mühendis İş İlanları